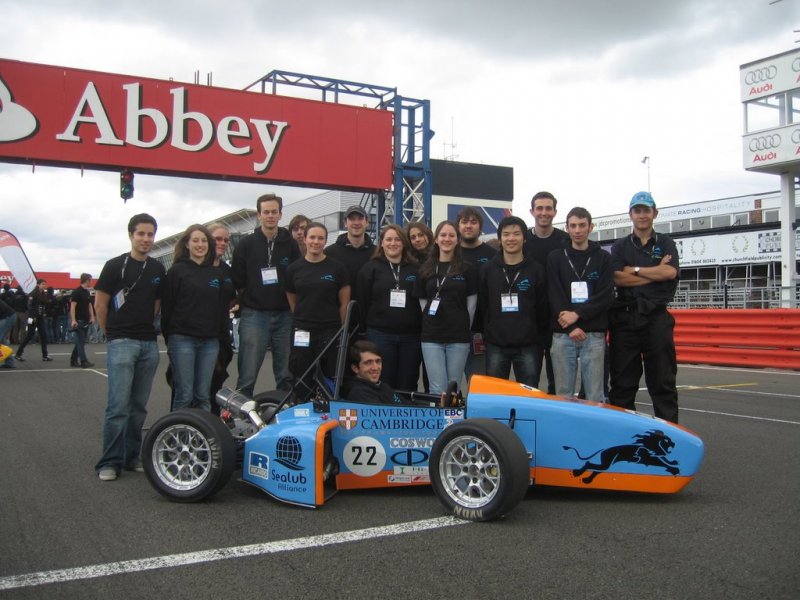
Formula Student UK 2009 - Competition Report
Thursday:
The team spent the day registering, queuing, queuing, queuing and more queuing…
This morning was spent preparing the car for technical inspection – mostly setup jobs such as brake system filling, reattaching components dismantled for travelling and systems checks. Inevitably with 93 teams at the competition, scrutineering was not going to be completed in a single day, and with ticket #64 Full Blue were unable to get through as hoped. It does reopen in the morning and so the team’s new aim is to get the car through technical inspection as quick as possible in the morning to maximise driver/car time, in preparation for the dynamic events starting on Saturday.
At the same time, tomorrow sees the static events take place – business, cost and design. These require the car and so must be juggled with technical inspection and testing, to ensure the car looks its best. Tonight we have to leave the pits at 10pm, followed be preparation for design judging tomorrow and an early(ish) night ready for the 7.00am start – drivers briefings and scrutineering queues beckon!
Friday:
Today saw the team pass though safety and technical inspections, as well as completing the static events for the competition.
Today the team had an early start to ensure they were at the front of the queue for scrutineering when it opened at 8.30am. Luckily some teams weren’t so quick off the mark and FBR were into scrutineering by 10am. Having passed safety inspection, the technical inspection was interrupted by having to attend the cost event.
The cost event tests the teams ability to consider how they would fulfil the brief of having to take their car design to market – consideration of manufacture, costs, feasibility and materials selection are all examined. This was shortly followed by the design competition – a detailed analysis by 9 professional automotive engineers, talking to members of the team regarding their designs, the decisions they came to and the justifications for those designs. Feedback from the judges was very positive and the team is excitedly waiting the results tomorrow.
The car then returned to scrutineering to pass with just modifications requiring tape, cable ties and a rubber glove! A great result and one that put the team back on track to be racing tomorrow. At the same time, members of the business team were presenting to a panel of 4 judges in the business presentation event. This is similar to a dragons den event, in which team members must sell the car to investors as if they were a start up company looking to sell around 1000 cars a year.
Having passed scrutineering, the car is now fuelled and managed to miss the tilt test by 30 seconds – ensuring that the team has an early start tomorrow to ensure that they can pass tilt test, brake test and noise test in time for the acceleration and skidpan events tomorrow morning. That is of course not before the late night, sorting out several electrical niggles – no rest for the racer…
Saturday:
FBR has a day of mixed emotions, as great results from the static event are overshadowed by a car failure. Today was always going to be close to the wire. The team was also awaiting results from the static events, in which it had aimed to improve on last year across the board.
The day started strongly – electrical problems now remedied the team passed tilt test first time (although not without a little verbal persuasion). From here noise test was the goal and the team returned to the pits to setup up the car. Promising noises from the engine quickly became a very loud bang as the engine sparked and backfired. Running a wasted spark system (two of the four spark plugs fire for every single engine ‘bang’) is susceptible to these happening, however on this occasion the throttle had been set in the wrong position – the intake took the full force of the explosion and effectively burst. Immediately the team was on the back foot and all hopes of passing brake and noise was put on hold, with entering any dynamic events at all today looking unlikely.
The team returned to the pits dejected, however as always ideas started bouncing around for solutions – we had 6 hours until the autocross event, what could we do by then?… A quick search around isolated two spare plenums in the pitlane. A team member was dispatched back to Cambridge to fetch a previous testing plenum, and a small huddle formed around the departed intake in an attempt to put humpty back together again. One brainstorming session later and the team had found its solution – a hybrid of old and new, with the help of some GFRP and plenty of ingenuity. Work began in earnest…
To buoy on the team the results of the static events were posted at the event HQ. They stand as follows:
Cost event: 12th overall Business event: 35th overall Design event: 36th overall
The team was delighted with these results, placing them safely in the top third of the 92 teams and improving considerably on all results from FSG last year. Feedback from the judges was encouraging – particularly noting the clear design choices and justifications made by the engineering team and the clever solutions found in the face of a relatively low budget (both financial and time). The cost team was complemented on its ‘almost perfect’ presentation, and particular interest was paid to the high quality of the suspension uprights (regularly photographed by judges throughout the paddock) and the ‘different’ plate wishbones (used for their low cost, accurate manufacture and short lead time).
But back to the pits… unfortunately the team missed acceleration, skidpan and autocross – a massive blow for a team that has set its goals high this year, but shown every sign of acheiving them until the last minute. Undaunted, the team has set its sights on completing the endurance event tomorrow – this will vindicate the mechanical design of the car and stand the team in good stead for the German competition (provided a more permanent intake solution can be found in time). And so I sit here with a new intake plenum, ready to go on the car first thing in the morning and to put Full Blue Racing firmly on the road to acheiving its overall aim of a top half finish at Silverstone.
Sunday:
Full Blue Racing bounced back from a tough Saturday to make it into the endurance run…
Having suffered a catastrophic failure yesterday, hopes were now set on making it into the endurance event so that track time could be maximised – the team is now looking to Hockenheim for the results wanted and any further data to backup work between now and FSG09 is valuable. The replacement plenum was finished overnight and fitted to the car first thing. Following some brief engine tuning the team then went onto pass noise test first time, and pass the driver egress test for Mike (our second endurance driver). From there the team had to perform a dance of the tyres whilst the weather constantly drifted from howling rain to bright sunshine. Wanting to maximise its chances for passing brake test, the team was keen to be on the right tyre at the right time.
Finally going with full wet tyres, the team congregated at the brake test area as the sun came out! With the track drying, Graeme (driver 1) did a great job of keeping the tyres cool with puddles and took the FBR09 its first steps. Brake test was passed! The SAFBR09 was ready to race, and the team had just one hour until it’s slot – perfect!
Further tweaks to the car were made in preparation for the endurance event, before the team queued up in the F1 pitlane to start the endurance event (held on the luffield and woodcote corners of the GP track). Finally, the team was off! Graeme performed well in what were now adverse conditions, on tyres that were by now struggling to keep the car on the track. The aim was to bring the car home and test durability, aiming to fix anything that showed signs of causing problems in the future. After 14km of faultless running the car came in for the driver change.
Unfortunately the forced re-use of a sump gasket when changing the oil (due to a lack of spare) had failed and the car was withdrawn with an oil leak. And so the UK competition was over for FBR, and the team is now taking forward the positives gained from the event. Design work has already started on a mk2 intake, with the aim of taking a fully tested part to Germany in two weeks. Spares will be sourced for the car to prevent unenecessary problems and small tweaks will be made to the car. Beyond this the team is overjoyed as the mechanical and electrical systems performed exactly as desired – it suggests a strong performance is within reach for the team in Germany, and with the team placing highest of those that only completed static events the team moves forward with a new wave of confidence. Thank you for keeping up to date with us – we’ll be back on here in a couple of weeks to let you know how we get on at Germany.